Ecostar is a Turkish manufacturing company with a 60-year history and a team of approximately 190-200 employees. They mainly produce burners, combustion systems and products such as condensing boilers, combi boilers and water heaters, both for industrial and domestic use.
The company has dedicated R&D and P&D departments to not only meet the needs of their clients but also to stay abreast of emerging technologies. Being a custom-manufacturing company that produces its own products, this strategic approach enables them to maintain a competitive edge.
Their factory is located in Çorlu and their headquarters is in Kartal.
Challenges
The client sought to streamline their production and sales operations through automation. The company's structure includes departments for domestic sales, exports, project contracting, after-sales services, production, planning, and logistics.
Prior to the implementation of the ERP system, they found themselves in a bit of a chaos. The majority of the company's processes were either paper-based or Excel-based, making them challenging to monitor and report on, which in turn negatively affected overall productivity. Furthermore, the ability to track the performance of sales representatives was identified as a crucial element for the company's growth.
As the company expanded, it became apparent that spreadsheets being used, was falling short in efficiency, prompting them to look for a more professional solution. Upon conducting thorough research, the company identified 1C as the ideal choice for their needs. Following a comprehensive evaluation, they implemented it and successfully completed the project.
Partner
Appviser PS
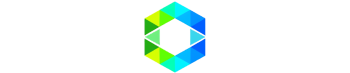
Appviser specializes in offering comprehensive software development and management/process consulting services. The primary objective is to enhance efficiency, stimulate decision-making mechanisms, and optimize business processes. Alongside the end-to-end ERP solutions, Appviser provides extensive support for essential processes by offering a range of modules, such as CRM, QDMS, Machine-Equipment Maintenance and Repair Tracking.
- support in Turkish, English, and Russian
- team members are Certified Public Accountants and graduates of Management Information Systems
Product
1C:Drive
Flexible and comprehensive ERP solution capable of automating the majority of processes in companies of any size. The software combines multiple capabilities to execute various business operations, manage production workflows, digitize paper streams, and connect companies to their partners. 1C:Drive helps companies to boost their growth and help stay competitive in the dynamic business environment.
Learn about 1C:DriveWhat was done
Process
During the implementation, the following business processes were automated:
Data analysis and reporting
Document management
Project management
Maintenance and repair
Customer success
“If I were to describe 1C:Drive in a single sentence, it would be that it presents an excellent balance between cost and the performance of the product itself. Up until now, I can sincerely say that, although we have utilized many programs aiming for ease of use, I have yet to encounter a program as intuitive and results-driven as 1C:Drive.
At the same time, we ramped up our efforts on 1C:Perform, one of the new technologies developed by 1C:Enterprise, alongside digitizing all of our client's processes. Our goal is to automate our clients' budgetary and financial workflows, and to create thorough reporting.”
Results
Related Customer Stories
Interested in 1Ci solutions?
Tell us about your project and we'll find the best 1Ci partner to help.